Thermal Calibration – Precision Testing for Temperature Accuracy
Why Thermal Calibration Matters?
- Temperature calibration is an essential practice to ensure the precision and reliability of temperature measurement instruments across various industries. It involves comparing an instrument’s temperature readings to a certified reference standard and making adjustments as needed to achieve accuracy.
- Precise temperature measurements are vital for quality assurance, safety, and meeting regulatory requirements, influencing industries such as manufacturing, food production, pharmaceuticals, and HVAC systems.
- Routine calibration of temperature sensors and instruments enables businesses to enhance operational efficiency, lower energy usage, and maintain superior product quality.
- It helps avoid problems stemming from inaccurate readings, such as substandard products, inefficient processes, and potential safety risks.
- Gaining a clear understanding of calibration techniques, the instruments involved, and the importance of proper documentation and traceability is key to upholding consistent measurement accuracy and reliability.
Why Choose Taurus for Thermal Calibration?
At Taurus, we provide professional thermal calibration services to keep your temperature instruments at peak performance. From furnaces and thermocouples to data loggers, our expertise ensures compliance, precision, and operational efficiency. Invest in reliable calibration to protect your process integrity and maintain superior product quality.
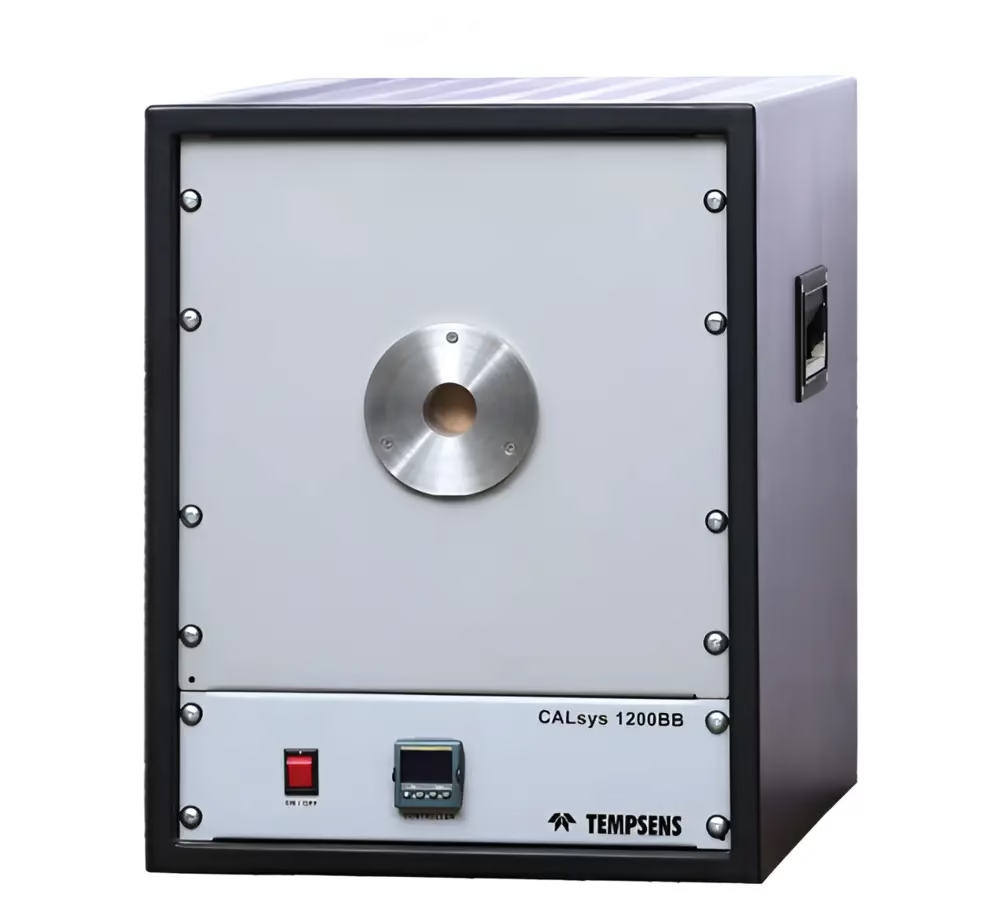
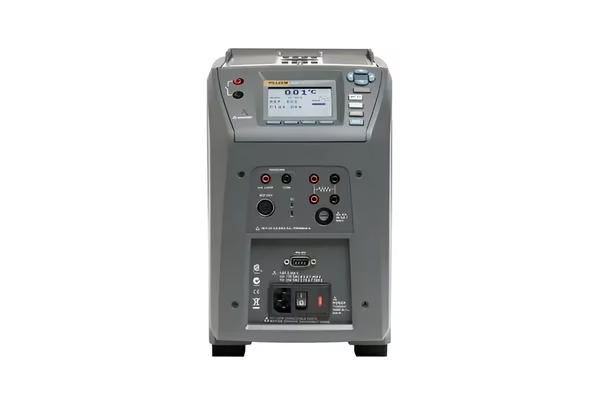
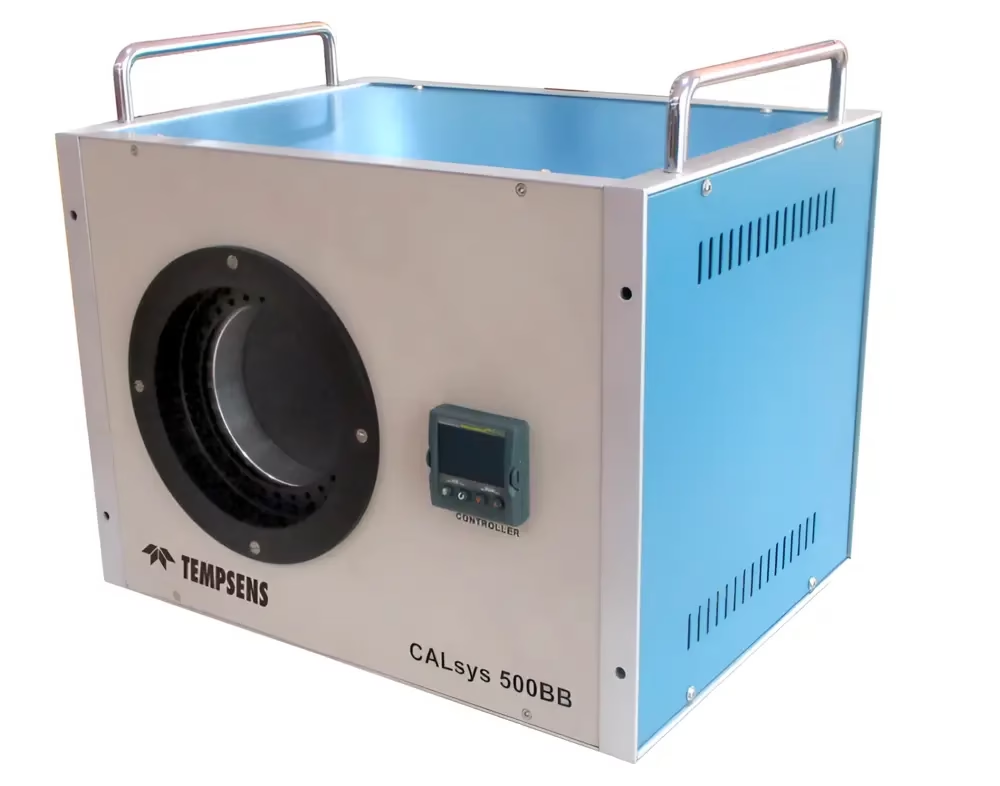

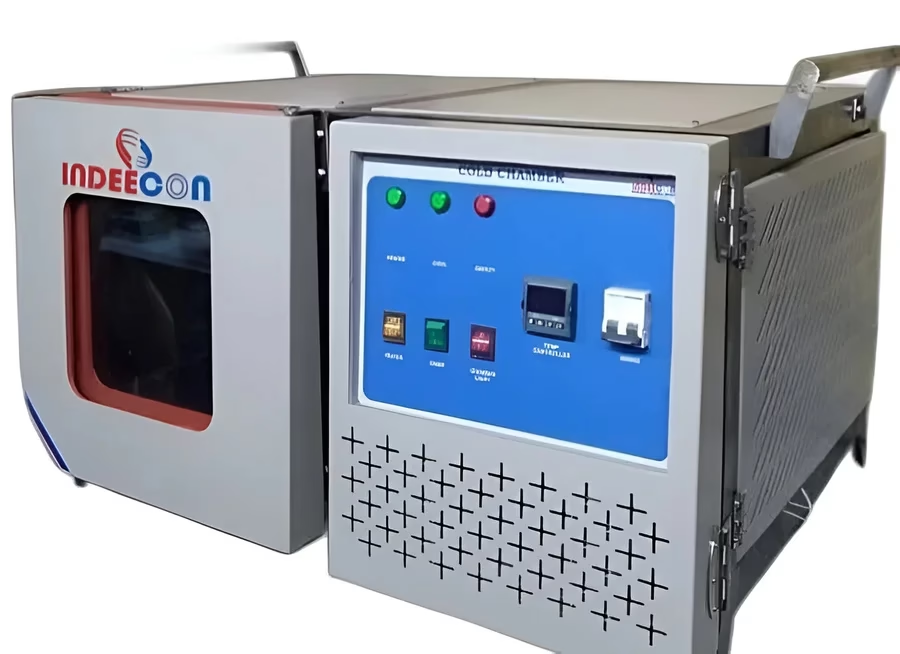
Thermal Calibration Features
(%RH, °C)
Why is Thermal Calibration Important?
Temperature calibration is vital for ensuring the precision and dependability of temperature measurements, which are critical for quality assurance, safety, regulatory compliance, and operational efficiency across numerous industries. Accurate temperature data helps maintain the integrity of processes and products. For example, in the pharmaceutical sector, precise temperature regulation is crucial to ensure the safety and effectiveness of medications. Errors in temperature readings can result in subpar products, leading to financial losses and potential health risks.
In industrial environments, calibrated temperature instruments are key to streamlining operations, reducing energy usage, and enhancing product quality. Failure to calibrate instruments properly or regularly can lead to:
- Inefficient processes
- Higher energy expenses
- Defective products
Moreover, regulatory agencies often mandate adherence to strict calibration protocols to meet safety and quality standards. Regular calibration ensures compliance, helping businesses avoid legal and regulatory complications.
How Often Should Thermal Instruments Be Calibrated?
The frequency of temperature instrument calibration depends on several factors, including usage patterns, the critical nature of measurements, manufacturer guidelines, environmental conditions, historical performance, and regulatory demands. Instruments used frequently or in applications requiring high accuracy typically need more frequent calibration. For example, temperature sensors in pharmaceutical production may require calibration every 3-6 months due to stringent regulations. Instruments with less critical roles or infrequent use might only need annual calibration.
Environmental factors also influence calibration schedules. Instruments subjected to extreme conditions, such as high temperatures, humidity, or corrosive environments, may need more frequent checks to ensure reliability. Additionally, historical performance data can guide calibration intervals; instruments prone to significant drift over time might need regular recalibration, while stable instruments may be checked less often.
Establishing a calibration schedule tailored to these factors ensures temperature instruments maintain their accuracy and reliability, supporting optimal performance and compliance.
Can I Perform Thermal Calibration Myself?
While basic temperature calibration can be handled in-house with appropriate tools and training, professional calibration services are strongly recommended for critical applications, stringent accuracy requirements, and adherence to regulatory standards. Professionals bring specialized expertise, advanced equipment, and traceability to ensure precise and reliable calibration results.
In-house calibration may suffice for routine checks or non-critical applications. However, for highly accurate measurements or compliance with industry regulations, professional calibration offers greater reliability and assurance. Services from providers like Fluke include on-site and laboratory calibration as well as traceable calibration certificates, ensuring that instruments meet the highest standards of precision and reliability.
Leveraging professional calibration services helps organizations maintain quality control, achieve regulatory compliance, and optimize operational efficiency.
- Initial Assessment: We evaluate your equipment to determine the appropriate calibration procedures.
- Testing and Verification: Our team performs in-depth testing to verify the performance of all systems.
- Adjustments and Repairs: If necessary, we make adjustments or repairs to ensure optimal functionality.
- Certification: Once calibrated, your equipment is certified to meet industry standards.
- Pharmaceuticals: Ensuring the safety and effectiveness of medications.
- Food Production: Maintaining the quality and safety of food products.
- Manufacturing: Ensuring precise temperature control in production processes.
- HVAC Systems: Verifying accurate temperature and humidity control.
Accuracy: Delivers precise measurements for reliable decision-making.
Compliance: Meets NABL and other international standards.
Documentation: Provides detailed reports for audit and compliance purposes.
Expertise: Our certified professionals ensure the highest level of precision.